My work
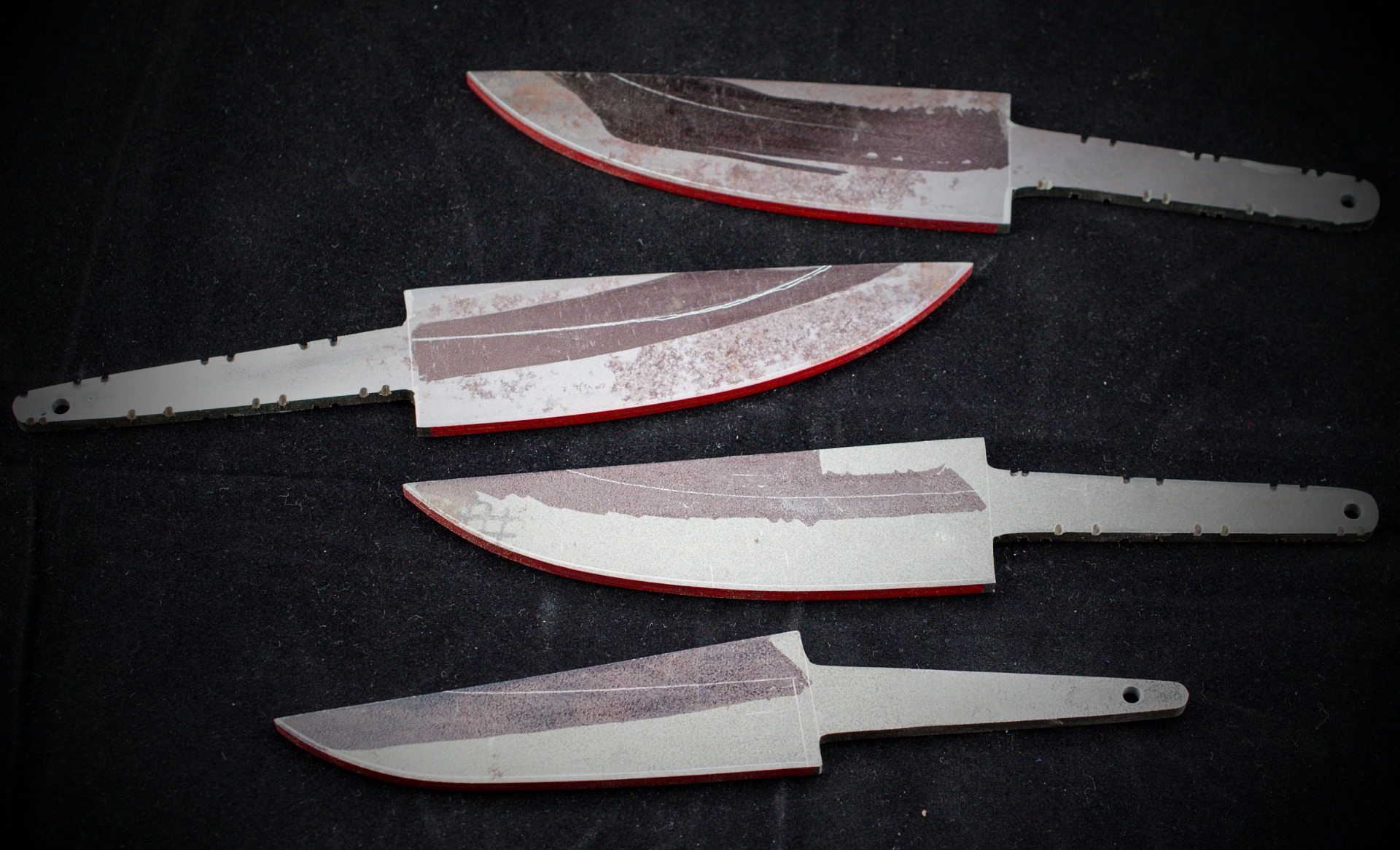
Steel
The basis for the production of the knife is quality steel and that is why I use the best:
RWL 34, Elmax, M390 - powder steel
N690 - tool cobalt steel
K110 (D2) - tool steel
I usually use a thickness of 3 - 5 mm.
Verified quality supplier:
www.nozirske-oceli.cz
Here I also have the finished blades professionally hardened to the required hardness. I will just add: absolute satisfaction!
I also have to recommend other, very well-functioning and equipped companies:
www.jatagan.eu, or from as far away as Finland: www.brisa.fi
In these shops you can really buy everything you need to make a knife, including tools and equipment for making cases or for stabilizing woody plants. You can also buy a ready-made blade.
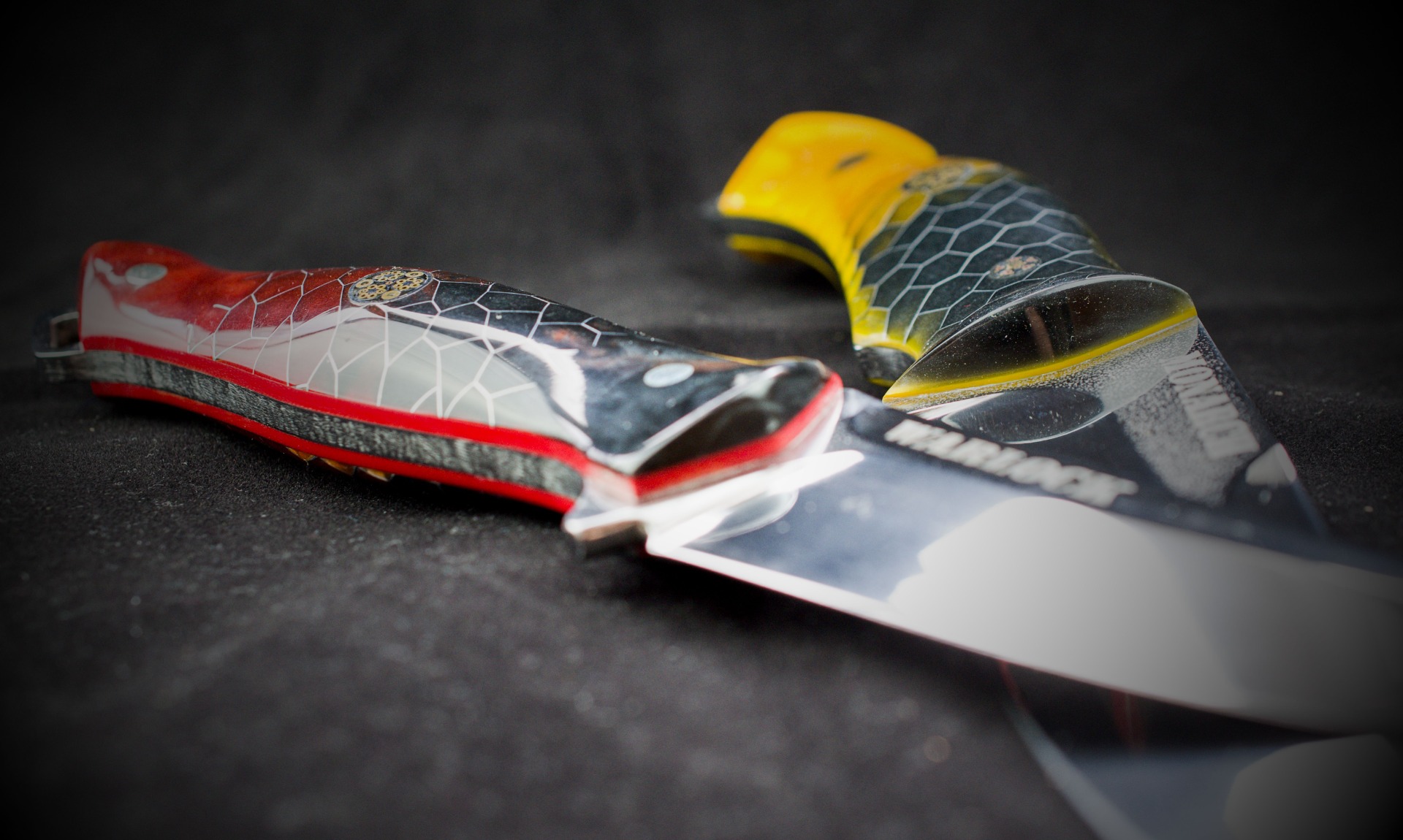
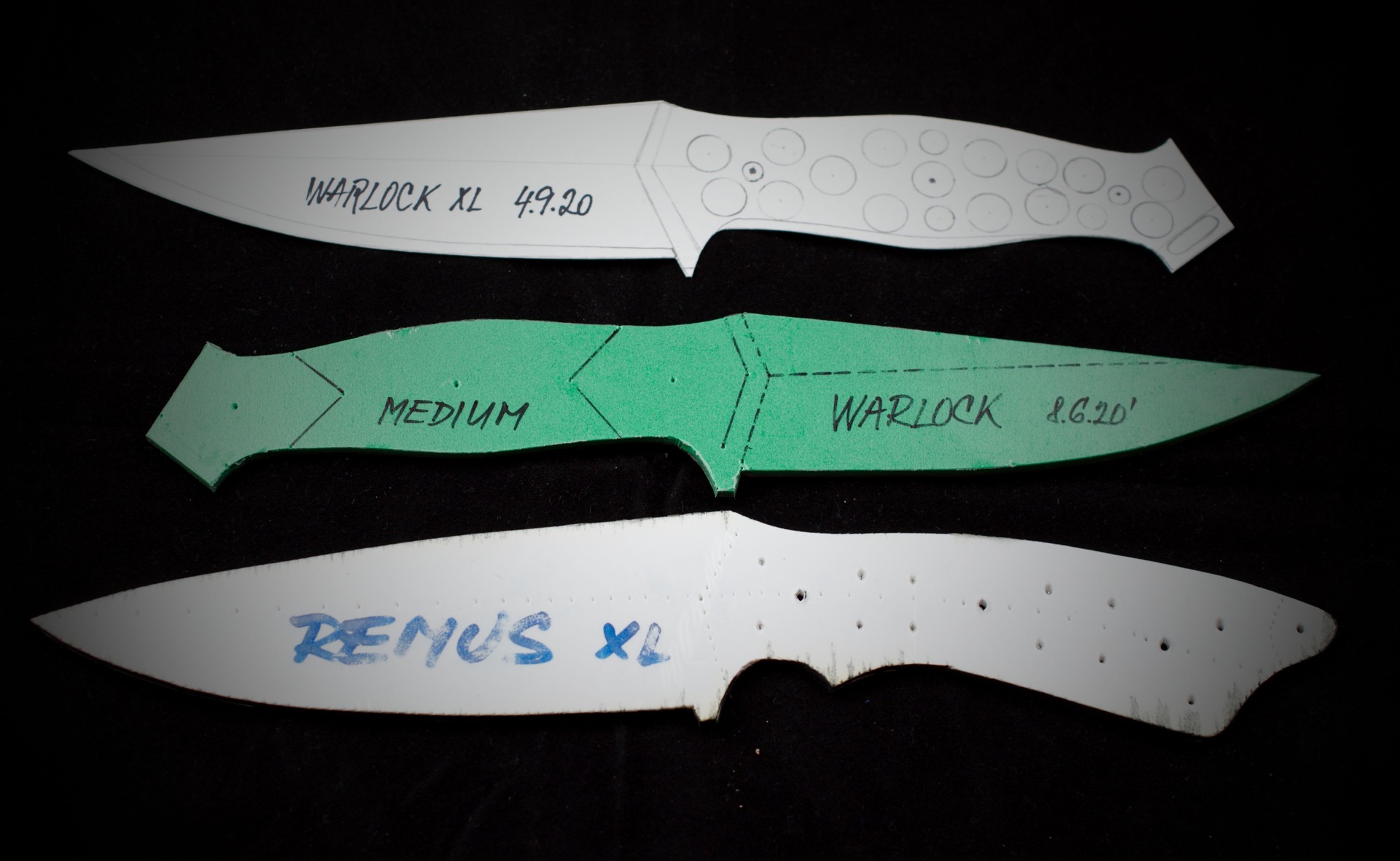
Knife blade
First, with the help of a template, we draw the chosen type of knife on a sheet of steel. I perform cutting with an angle hand grinder. I recommend thin, cutting discs. Care must be taken to ensure that the steel does not overheat (cool with water). I already perform the shape of the blade and the alignment of the edges on a belt grinder (sanding belt - grain size 60).
And the most important thing comes - the cut. (bad cut = bad knife). I use a special tool for cutting the blade and control the angle with a digital protractor.
This ends the machine work and begins a long process of manual grinding and polishing ... as well as constant inspections. The prepared blades then go to the tempering plant and after returning I perform "etching" (etching of marks) and the final finishing of the blade to a mirror finish.
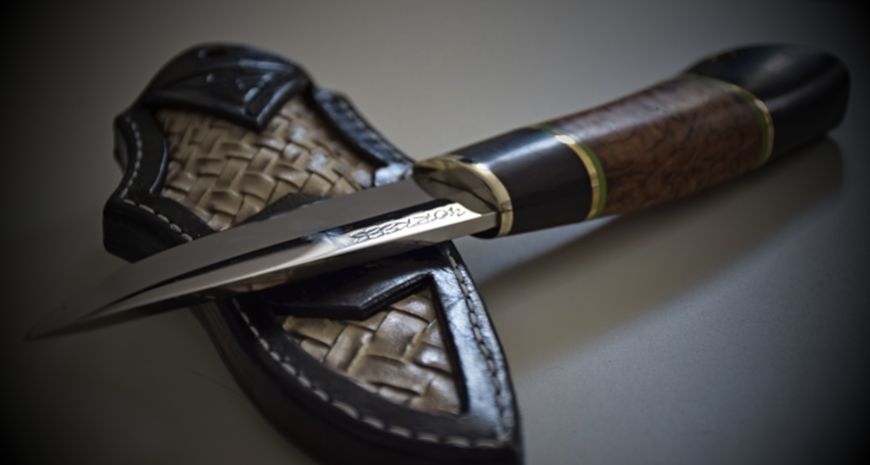
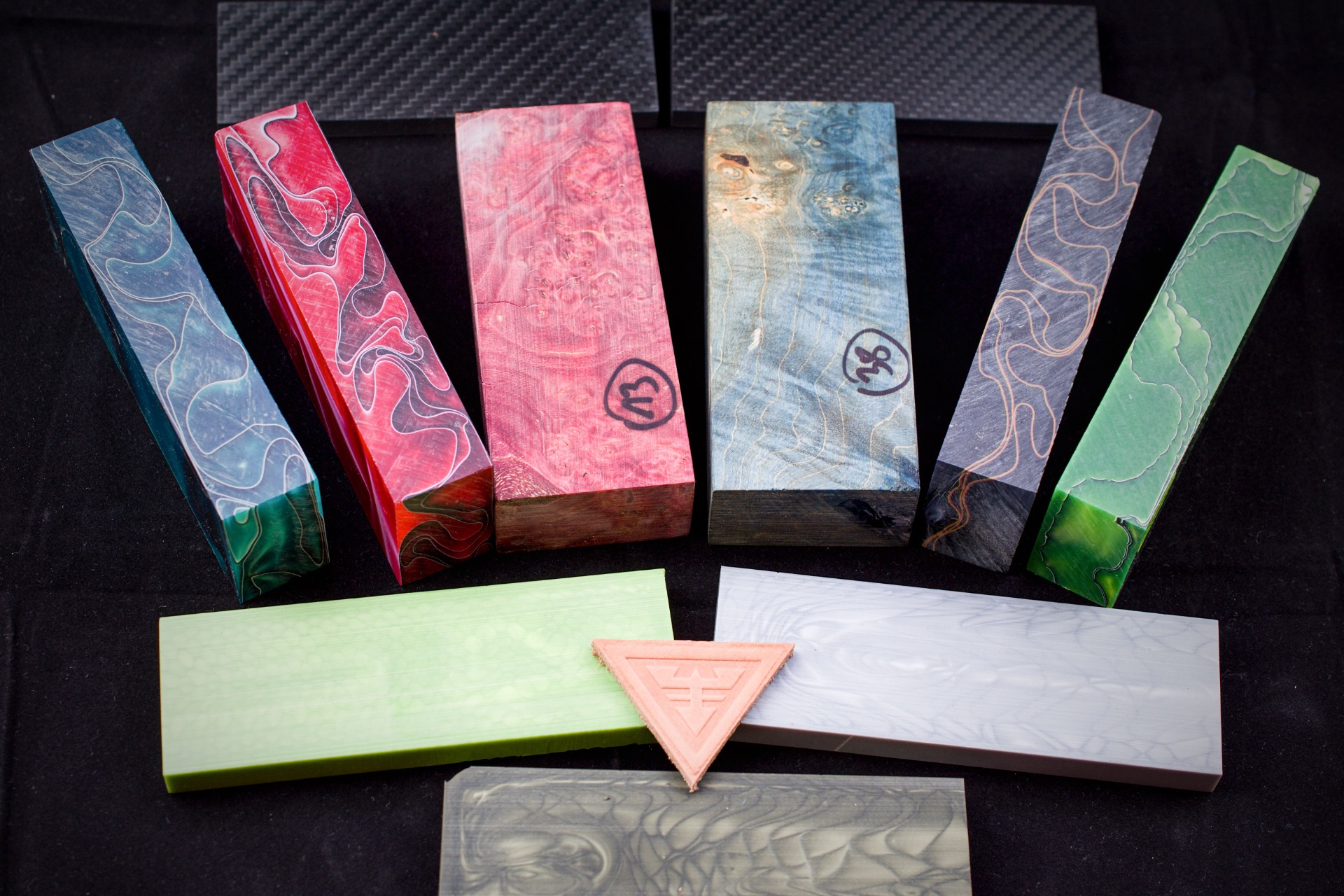
Knife handles
I most often use stabilized wood, I perform stabilization myself, or I buy from my friend Max Netrval
I also really prefer casting resin (epoxy resin) with encapsulated aluminum honeycomb, I will really win :-)
For woods, I prefer exotic woods and spices, including Finnish birch.
The offer of the mentioned stores then includes an inexhaustible amount of acrylates, G10, carbon, etc., so everyone will surely choose.
I must also not forget the antlers preferred by hunters and the handles made of leather strips.
I also use stainless steel, alpaca, fiber, G10 and occasionally brass. I really liked mosaic pins (rivets).
Well, the assembly of the handle and the blade requires a really good connection, so if the glue, so: UHU Plus Endfest 300kg.
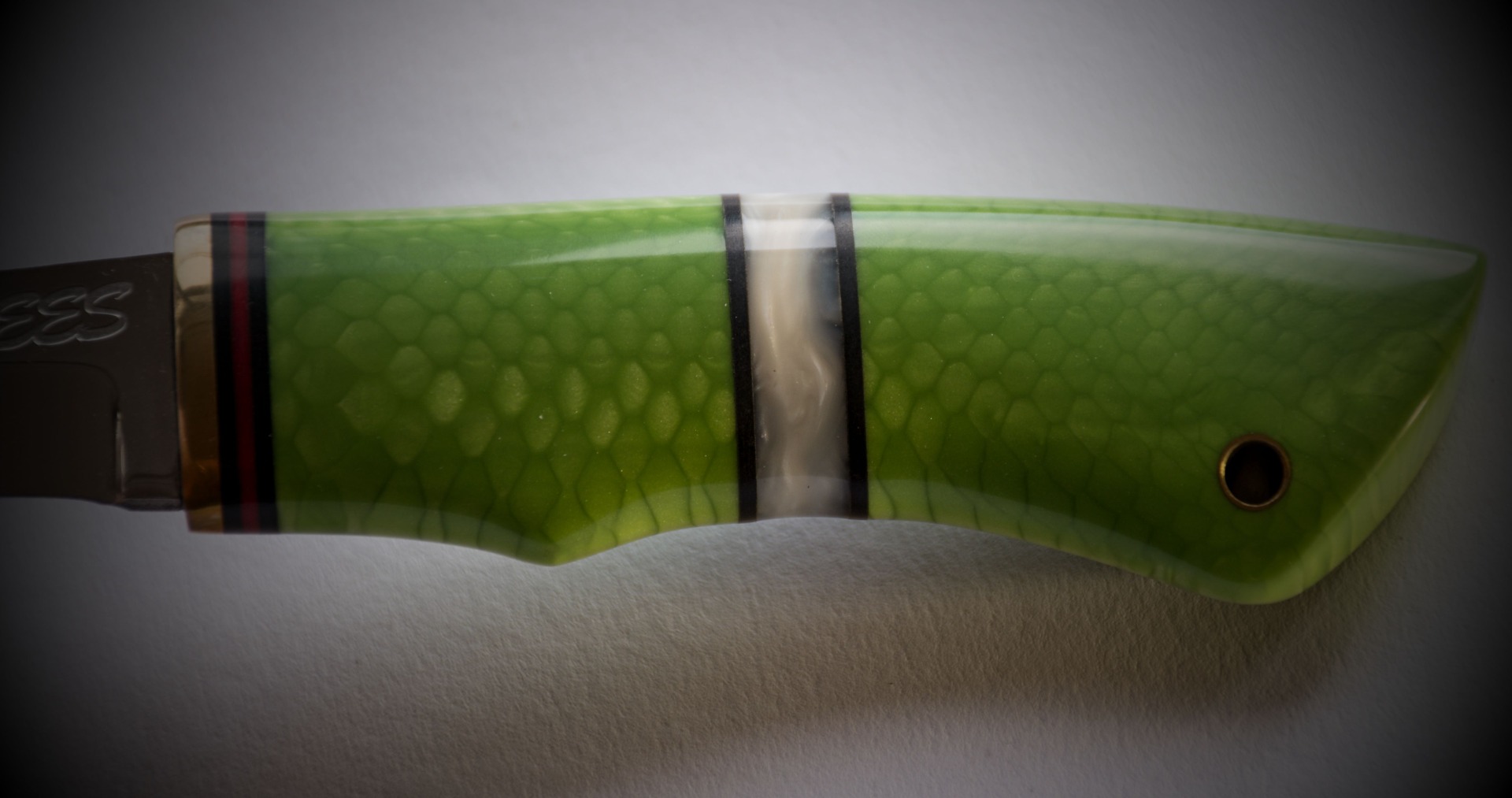